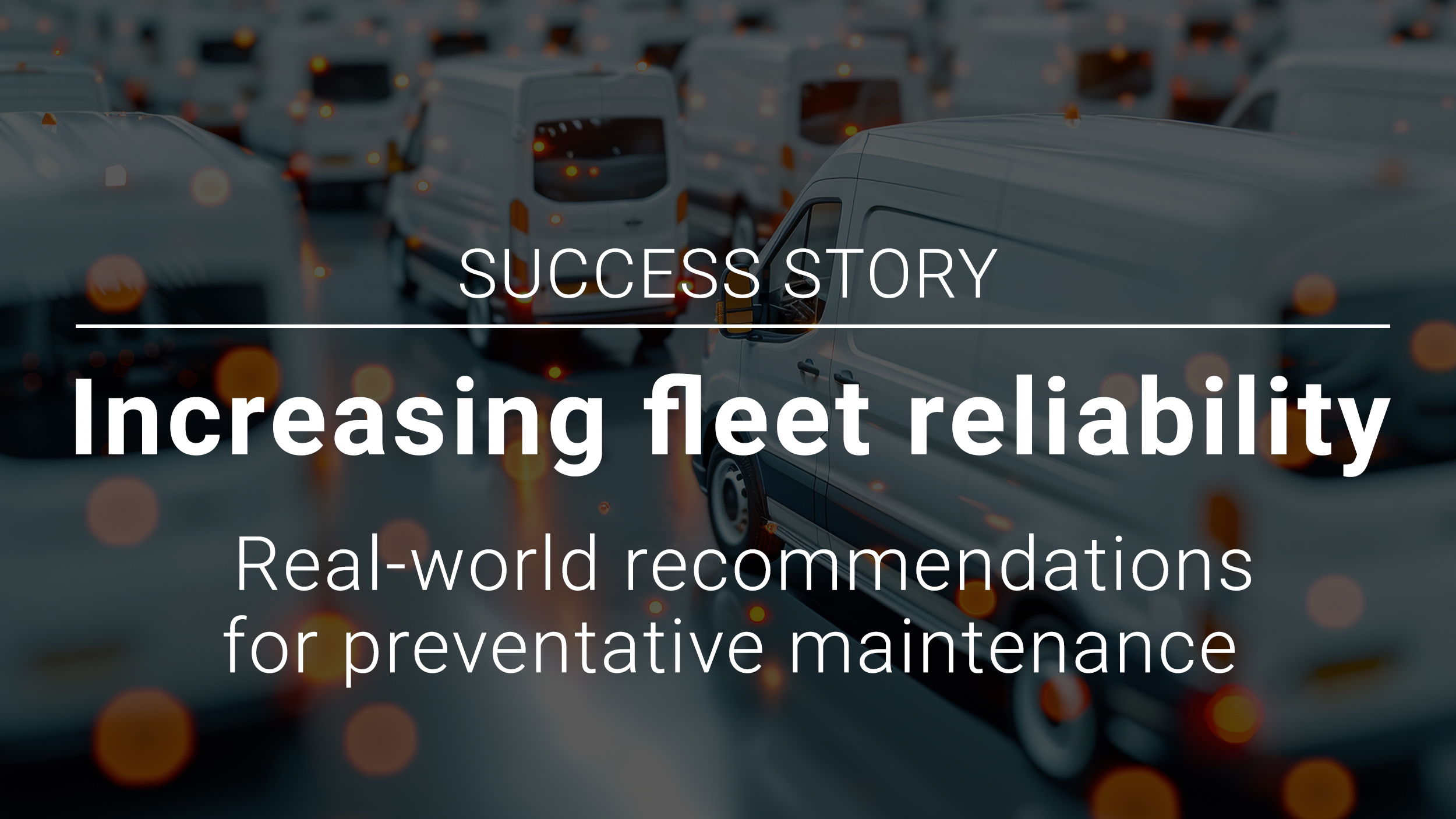
Addressing rising costs and inefficiency
The logistics partner for a multinational e-commerce company faced two key challenges as their fleet of vehicles approached the five-year mark—when warranties on many of their vehicles would expire:
In short, our logistics client needed a solution that could quantify the financial risk associated with maintaining their fleet post-warranty and propose a preventative maintenance plan that would extend vehicle lifespans, reduce downtime, and improve reliability, all while being cost-effective.
Addressing rising costs and inefficiency
The logistics partner for a multinational e-commerce company faced two key challenges as their fleet of vehicles approached the five-year mark—when warranties on many of their vehicles would expire:
In short, our logistics client needed a solution that could quantify the financial risk associated with maintaining their fleet post-warranty and propose a preventative maintenance plan that would extend vehicle lifespans, reduce downtime, and improve reliability, all while being cost-effective.
Insights for data-driven maintenance
We approached the client’s logistics team with a data-driven, advanced risk modeling solution that leveraged our expertise in the automotive sector and our ability to work with OEMs to obtain critical warranty data. The solution combined statistical techniques—specifically a reliability analysis—with practical recommendations for vehicle maintenance.
The key to our solution was that it not only helped our client optimize maintenance costs but also allowed them to plan for parts and services more effectively. By reducing unplanned downtime and minimizing the need for emergency repairs, they could maintain fleet reliability while cutting costs.
Insights for data-driven maintenance
We approached the client’s logistics team with a data-driven, advanced risk modeling solution that leveraged our expertise in the automotive sector and our ability to work with OEMs to obtain critical warranty data. The solution combined statistical techniques—specifically a reliability analysis—with practical recommendations for vehicle maintenance.
The key to our solution was that it not only helped our client optimize maintenance costs but also allowed them to plan for parts and services more effectively. By reducing unplanned downtime and minimizing the need for emergency repairs, they could maintain fleet reliability while cutting costs.
Benefits of a preventative maintenance model
While the full preventative maintenance strategy has not yet been implemented across their entire fleet, the results from our model have already provided significant insights:
Cost savings
By following our recommendations, they could avoid up to an estimated $13 million in spend annually just by reducing the frequency and cost of major repairs in critical vehicle components.
Financial risk mitigation
Our calculations indicated that without preventative measures, our client would face a 227% increase in repair costs once warranties expired. While this increase cannot be substantially reduced, our focus is on making this out-of-warranty jump as small as possible. Our preventative maintenance schedule provided a clear path to reducing these future liabilities.
Improved reliability
The reliability modeling showed that implementing our maintenance schedule would significantly improve vehicle reliability, leading to less downtime and more efficient operations.
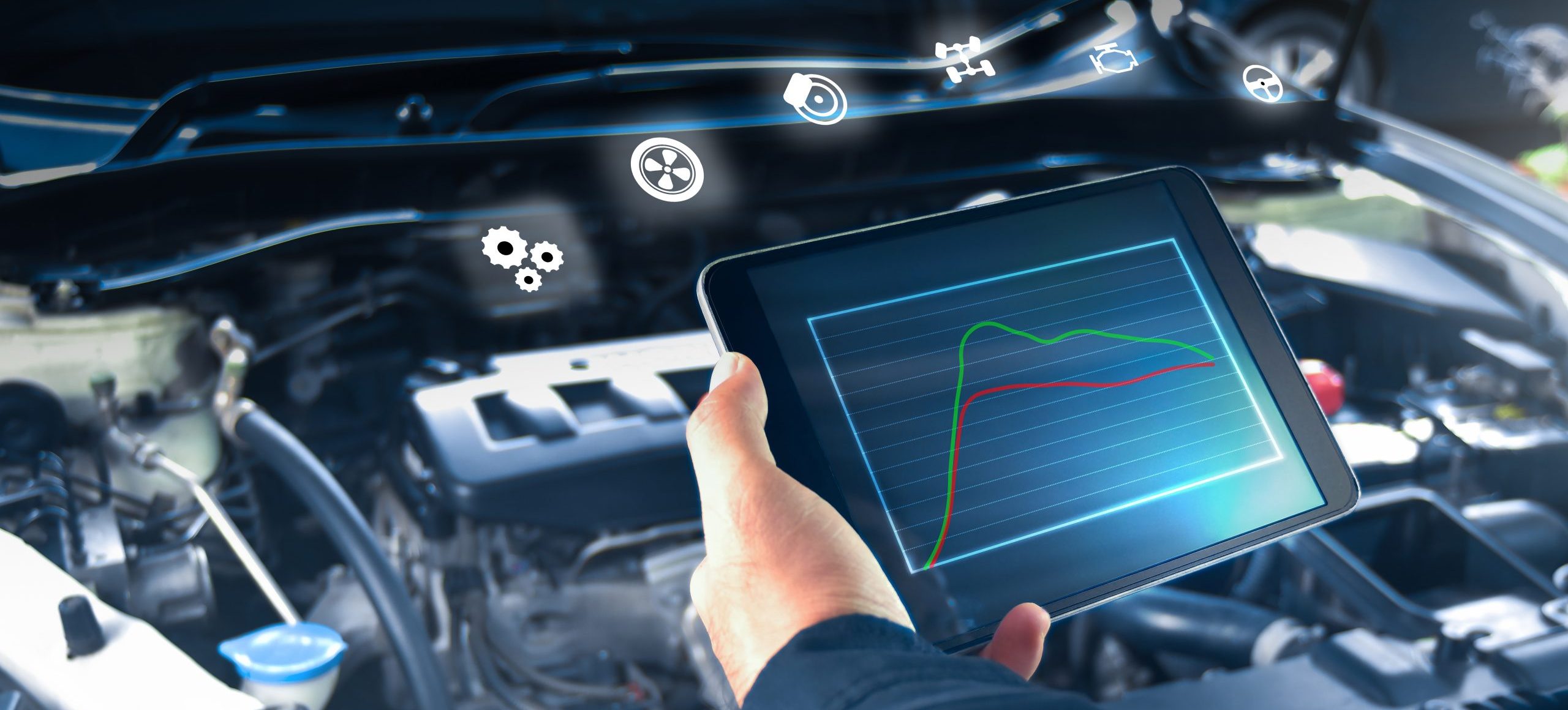
Benefits of a preventative maintenance model
While the full preventative maintenance strategy has not yet been implemented across their entire fleet, the results from our model have already provided significant insights:
Financial risk mitigation
Our calculations indicated that without preventative measures, our client would face a 227% increase in repair costs once warranties expired. While this increase cannot be substantially reduced, our focus is on making this out-of-warranty jump as small as possible. Our preventative maintenance schedule provided a clear path to reducing these future liabilities.
Cost savings
By following our recommendations, they could avoid up to an estimated $13 million in spend annually just by reducing the frequency and cost of major repairs in critical vehicle components.
Cost savings
By following our recommendations, they could avoid up to an estimated $13 million in spend annually just by reducing the frequency and cost of major repairs in critical vehicle components.
The foundation for long-term savings
The project has provided our client with a clear understanding of future maintenance costs and the advantages of a structured preventative maintenance plan. To see the full benefits, they need to implement and operationalize the recommended maintenance activities. The methodology and tools we provided give them a solid foundation to continue optimizing their fleet management strategy.
This project exemplifies the power of data-driven decision-making in fleet management. By combining advanced risk modeling and preventative maintenance strategies, we provided this organization with the tools to optimize their fleet maintenance, reduce operational costs, and enhance vehicle reliability. Although the full operational results are yet to be realized, the financial and strategic framework we’ve put in place gives them a clear path to achieving longterm savings and efficiency gains.
The foundation for long-term savings
The project has provided our client with a clear understanding of future maintenance costs and the advantages of a structured preventative maintenance plan. To see the full benefits, they need to implement and operationalize the recommended maintenance activities. The methodology and tools we provided give them a solid foundation to continue optimizing their fleet management strategy.
This project exemplifies the power of data-driven decision-making in fleet management. By combining advanced risk modeling and preventative maintenance strategies, we provided this organization with the tools to optimize their fleet maintenance, reduce operational costs, and enhance vehicle reliability. Although the full operational results are yet to be realized, the financial and strategic framework we’ve put in place gives them a clear path to achieving longterm savings and efficiency gains.
Fast facts
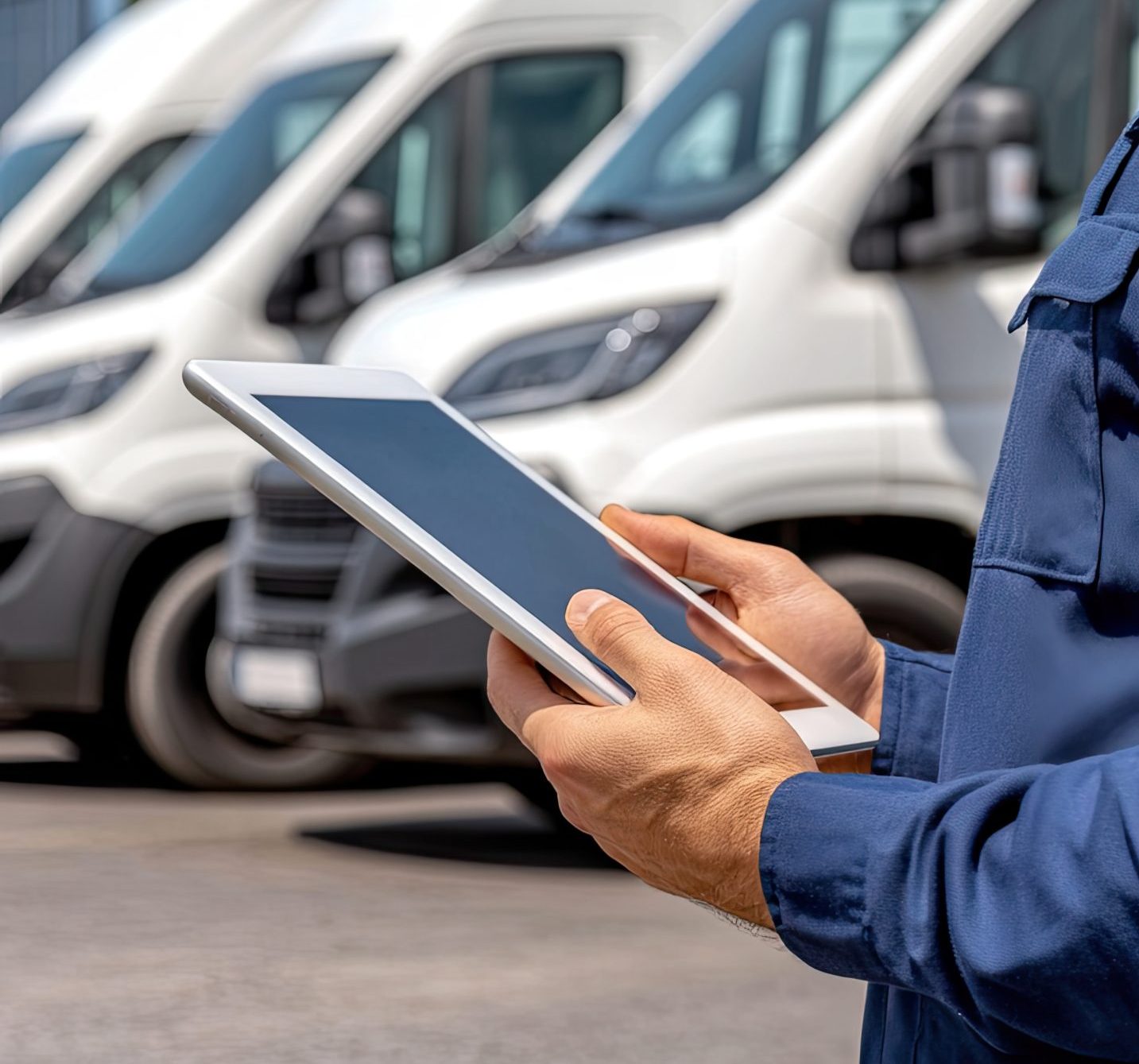
Customer: Middle-mile logistics partner for a multinational e-commerce company
Business Opportunity: Challenge: Faced with rising maintenance costs and inefficient scheduling as their vehicle warranties expired, our client needed a tailored preventative maintenance plan to reduce costs, extend vehicle lifespans, and improve reliability.
Geographical coverage: United States
Solutions implemented: MSX developed a data-driven risk modeling solution, using warranty data and survival analysis to create a preventative maintenance schedule. This approach aimed to reduce repair costs, extend vehicle lifespans, and improve reliability, potentially avoiding up to an additional $13 million in spend annually. knowledge.
Fast facts
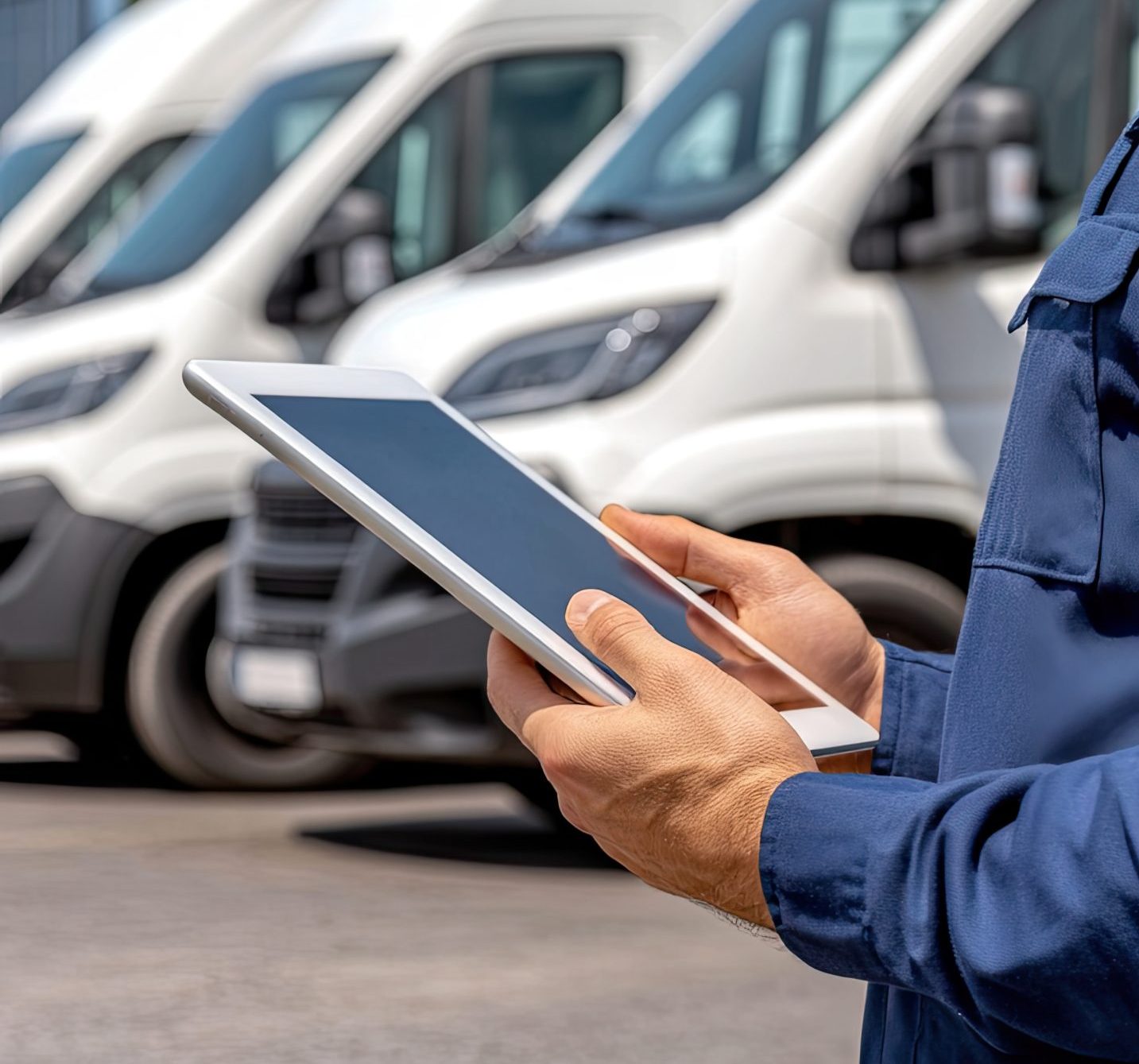
Customer: Middle-mile logistics partner for a multinational e-commerce company
Business Opportunity: Challenge: Faced with rising maintenance costs and inefficient scheduling as their vehicle warranties expired, our client needed a tailored preventative maintenance plan to reduce costs, extend vehicle lifespans, and improve reliability.
Geographical coverage: United States
Solutions implemented: MSX developed a data-driven risk modeling solution, using warranty data and survival analysis to create a preventative maintenance schedule. This approach aimed to reduce repair costs, extend vehicle lifespans, and improve reliability, potentially avoiding up to an additional $13 million in spend annually. knowledge.